Is the instrument really broken, or does it just need to be optimized?
Laboratory instrumentation always seems to go out of service at the most inopportune times. Who hasn’t been faced with an equipment issue just before starting a new screen, or perhaps discovered an issue right after a critical addition? For robotic liquid handling systems, often integral to a process, “out-of-service” can be a common occurrence. But is the instrument really broken, or does it just need to be optimized?
During a recent applications visit (during which the Artel technical rep’s task was to optimize a group of liquid handlers for specific assays), a customer expressed frustration over results he was getting for a particular assay: CVs of over 15%. Was the error originating from his liquid handlers, or from the components of the assay itself? The technical representative suggested some adjustments to the pipetting parameters to more effectively control the liquid handler performance – eliminating the instrumentation as the source of the error. In this case, the optimization step reduced the CVs for the assay to an acceptable level, reduced the amount of additional troubleshooting required and allowed the customer to get back to his regular work.
The moral of this story: we have learned that “not working” does not necessarily mean broken. Instead, an out-of-service event sometimes simply means the instrument has not been optimized for this specific assay. Troubleshooting considerations should include the fit between the liquid type and volume and the pipetting technology, liquid handler settings, and labware quality.
Here are a few considerations to help steer your investigation and aid in optimizing your pipetting methods:
1. Pipetting Technology
The most appropriate pipetting technology will be largely dependent on your process. While you may be tempted to switch to a new approach, you may consider the following characteristics:
- Air Displacement: Air gaps are large, which causes variability due to air compression and changes in temperature.
- Result: Poor precision and accuracy for low volumes
- Positive Displacement: Air gaps can be very small and because liquid is less compressible than air, dilution may occur if the air gap between the fluid and sample breaks down.
- Result: Better precision and accuracy
2. Liquid Class Settings
What type of liquid and corresponding liquid class was used? Each liquid type dispensed will likely require different liquid handling settings which will make up a separate liquid class. The following best practices for liquid types describe how to achieve improved liquid handling performance.
Volatile Liquids (High Vapor Pressure)
- Use Reverse (Waste) Mode pipetting
- Aspirate slowly
- Reduce system air gap
- Saturate system air gap
- Chill reagents if possible
Low Viscosity / Low Surface Tension
- Use Reverse (Waste) Mode pipetting
- Minimize dispense speed
- increase transport air gap
High Viscosity Liquids
- Use Reverse (Waste) Mode pipetting
- Aspirate & dispense slowly
- Increase syringe pump delays
- Warm reagents if possible
Small Volumes (<20µL) / High Reagent Cost
- Use Blowout Mode
- Minimize dispense speed
- Decrease syringe size
3. Pipetting Tip Selection
Are you using the correct disposable tips? Tip quality can dramatically affect the performance of liquid handling equipment. While generic tip prices can be very attractive, their use could add cost by sacrificing quality:
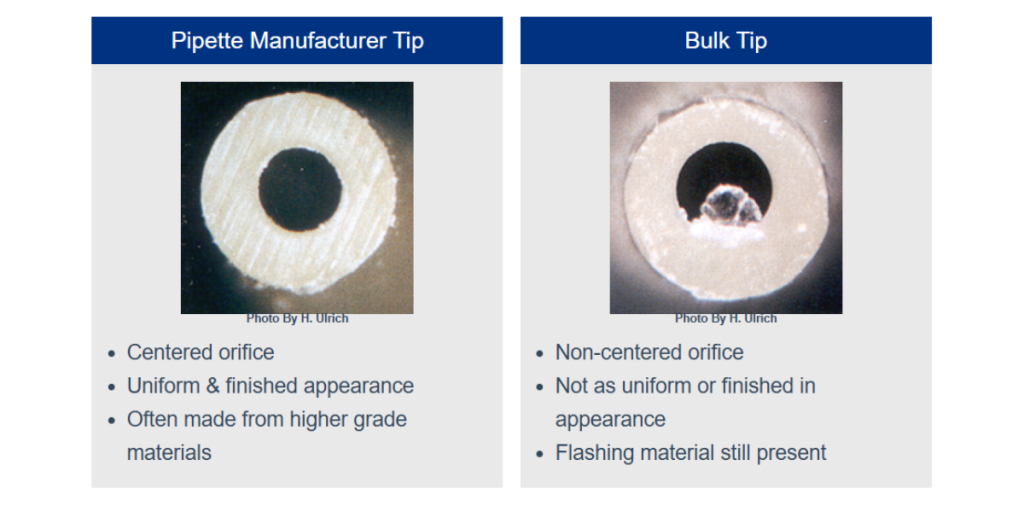
Pipette Manufacturer Tip
- Centered orifice
- Uniform & finished appearance
- Often made from higher grade materials
Bulk Tip
- Non-centered orifice
- Not as uniform or finished in appearance
- Flashing material still present
Characterizing the source of the errors can help you determine how to correct them. Ultimately, while liquid handling error is only a part of the overall error in your assay results, reducing the contribution from automation can pay off. Understanding and controlling liquid handling performance can indicate:
- when the instruments are due for periodic service
- which instruments are better for specific tasks than others
- when error mitigation could help avoid instrument failure, as a device approaches an action limit
Control of liquid handler variability can improve liquid delivery consistency and allow you to focus on other sources of error that may be affecting your results.